Нержавеющая ствольная сталь № 416: хорошее и плохое.
Введение
Нержавеющие стали начали применяться сравнительно недавно, будучи разработанными и введенными в технологические процессы лишь в последнюю сотню лет. В 1904-1909 годах французские и немецкие металлурги опубликовали свои базовые результаты по некоторым сплавам на основе железа, содержащим от 13 до 17% хрома (Cr) и от 0,12 до 1% углерода (С). Они определили, что атомы хрома на поверхности такой стали вступают в реакцию с кислородом воздуха и образуют очень тонкую пассивную (не подверженную коррозии) пленку оксида хрома. Наконец изготовители стали нашли решение (хотя и не такое недорогое) для разрешения проблемы ржавления стали. Эти новые хромистые стали начали называть inoxidable по-французски, rostfrei по-немецки и stainless по-английски. Было найдено, что такая пассивность возникает только если содержание хрома 10,5% и более, и если сталь содержит меньше, она не является на самом деле «нержавеющей». С 1910 года различные типы этой новой стали интенсивно изучались и разрабатывались по обе стороны Атлантики. Один из таких типов, называемый «мартенситным», оказался поддающимся закалке, как большинство обычных сталей: так нагрев до глубоко красного цвета с последующим охлаждением водой создавал прочный и твердый металл с ферромагнитными свойствами. Вскоре было открыто, что все типы нержавеющих сталей трудно поддаются механообработке. Тем не менее, в 1928 году американец Фрэнк Палмер открыл, что добавление небольшого количества серы в один из популярных типов мартенситной нержавеющей стали № 410 делает ее намного проще в обработке – создает легко удаляемую ломкую стружку, лучшие частоты вращения, долговечность инструмента и чистоту поверхности. Изобретение Палмера легло в основу стандартизации «легкообрабатываемой» нержавеющей стали №416, которая содержит 12,0%-14,0% Cr, 0,15% или больше серы (S), 0,15% С, 1,25% марганца (Mn), 1% кремния (Si), 0,060% фосфора (Р), и остальное железо (Fe). Разновидность №416-й, содержащей селен (Se), №416Se, разработанная позже, содержит 0,15% или больше Se и 0,060% серы. Сера в №416 реагирует в основном с марганцем и частично с железом и хромом, создавая гранулы обогащенных марганцем сульфидов, близких по структуре к MnS. Эти молекулы MnS мягкие, хрупкие и имеют слоистость (поверхности, вдоль которых они легко расслаиваются) в трех направлениях. Эти свойства придают №416 ее легкообрабатываемый характер. В №416Se формируются зерна селенидов, которые действуют также в процессе обработки. Минимальное содержание серы, которое характерно для ствольной ружейной стали 416, дает около 0,8% объема гранул MnS. Здесь необходимо отметить, что нержавеющая сталь №410, прародительница №416, не содержит серы, не содержит гранул MnS и поэтому трудно обрабатывается. По моим данным, никто из изготовителей стволов еще не сделал матчевых стволов из №410 (хотя некоторые пытались).
Многие кустарные изготовители стволов, а также некоторые крупные ружейные фабрики делают стволы из №416 – в основном в целевых и варминт конфигурациях – в больших количествах начиная с 1950-х годов. В общем, никаких других нержавеющих сталей для изготовления стволов не применяется. №416 является стандартной в промышленности, и поэтому многие стрелки считают, что это замечательная сталь для винтовочных стволов. В некоторых случаях ответ «Да», а в некоторых – «Нет», как мы увидим позже.
Репутация и свойства №416
Давайте посмотрим на №416 (и на очень похожую №416Se) более пристально. Вот несколько ссылок. Вот большой 40-страничный очерк по сталям в сборнике The 1997 Precision Shooting Annual, который я написал для стрелков из винтовки (не для металлургов). В общей литературе это ASM Specialty Handbook: Stainless Steels, J.R. Davis, Ed., опубликованная в 1994 году Американским Обществом Металлов (ASM), телефон 800-336-5152, это основная ссылка. Другие источники информации от ASM International это Metals Handbook, Desk Edition и Steels: Heat Treatment and Processing Principles, автор G.Krauss. (Заметка: технические книги вроде этих не дешевы, стоят около $150-$200).
Что же на самом деле представляет собой нержавеющая сталь№416? Она, как и другие стали, кристаллообразна и состоит из крошечных зерен низкоуглеродистой фазы Fe-Cr и из (менее чем 1% объема, как указано выше) обогащенного марганцем сульфида. Зерна очень плотно упакованы, и выглядят под микроскопом как будто бы они срослись вместе (что на самом деле правда), и имеют практически нулевую пористость. Под «кристаллообразной» я подразумеваю, что множество сферических атомов, составляющих каждое зерно, упакованы вместе в строгой геометрической структуре (или решетке), которая выстраивается на протяжении всего зерна. Из-за такого регулярного построения атомов мы называем зерна «кристаллообразными», или имеющими кристаллическую структуру, хотя зерна не имеют кристаллических поверхностей – как мы можем видеть на минеральных кристаллах выставочного типа, которые вырастают на открытых выемках. Заметьте, что эти кристаллообразные зерна не являются «молекулами» или «молекулярными». некоторые (малообразованные) оружейные писатели, которые пишут «молекулярная структура» стали, заставляют меня лезть на стену (и писать очерки, такие как этот).
Fe-Cr фаза нержавеющей стали может формироваться в одну из трех возможных форм построения своих атомов, или кристаллических решеток. Это 1) объемно-центрированная кубическая структура (ОЦК), где основная сборная единица сферических атомов Fe и Cr представляет собой восемь атомов, лежащих в углах воображаемого куба, а девятый в его центре (смотри фото модели из мячей для гольфа); такая решетка или кристаллический тип называется «феррит»; 2) гранецентрированная кубическая структура (ГЦК), где восемь атомов лежат по углам воображаемого куба, и шесть дополнительных атомов лежат в центре каждой грани куба (смотри фото модели; заметьте: в центре куба атома нет); эта решетка названа «аустенит» в честь британского металлурга Робертса-Аустена; и 3) объемно-центрированная тетрагональная (ОЦТ), которая похожа на объемно-центрированный куб, за исключением того, что воображаемый куб сплюснут в прямоугольный параллелепипед (мы увидим почему он короче); этот тип кристаллической структуры или решетки называется «мартенситом» в честь Прусского железнодорожного инженера и по совместительству исследователя металлов Адольфа Мартена. Эти три кристаллических типа – феррит, аустенит и мартенсит – имеются во всех видах сталей (и не только сталей) и являются базовыми термическими и физическими свойствами стали.
В №416 феррит, фаза ОЦК, стабильна при температурах меньше чем 1650°F. При нагреве до 1700°-1850°F ферритовые зерна трансформируются за время от минут до нескольких часов в аустенитовые зерна, фазу ГЦК. (заметьте: эта трансформация возникает из-за диффузного движения отдельных атомов и называется «диффузной» трансформацией). Очень горячие аустенитовые зерна №416 при быстром охлаждении (или закалке) как на воздухе, так и в масле трансформируются или изменяются практически молниеносно (при порядка 660°-480°F) до мартенситовых зерен или фазы ОЦТ. Эта быстрая трансформация носит «вытеснительный» характер и происходит не из-за диффузии атомов, а из-за массивного перемещения или сдвига аустенитовой решетки ГЦК в ОЦТ мартенситовый тип. (это «мартенситовый переход», который особенно важен при изготовлении очень прочных сталей из многих различных композиций). 0,15% углерода в стали №416 играет особую роль в ее трансформации от феррита через аустенит к мартенситу (как и в многих других типах сталей). Так как атомы углерода С (0,07 нм в диаметре, где1 нм = одна миллиардная метра) меньше, чем атомы Fe (0,126нм в диаметре) и атомов Cr (которые имеют приблизительно такой же размер), они слишком велики, чтобы удерживаться внутри межатомных пространств (или промежутков) ОЦК решетки или феррита. В ферритных сталях углерод просто комбинирует с железом и хромом в виде отдельных углеродных зерен. Однако промежутки в аустенитной структуре довольно велики, чтобы принять атомы углерода: в отличие от центра решетки ОЦК, центр ГЦК не имеет атома (смотри фото моделей). При трансформации ферритной стали в аустенитную при высокой температуре ее углеродистые зерна разрушаются, и свободные атомы углерода переходят в эти небольшие пространства в аустенитной решетке – мы называем это «растворением» углерода в аустенитных зернах. Что же происходит с растворенными в аустените атомами углерода при фазовом переходе в мартенсит? Трансформация смещения в мартенсит происходит так быстро, что атомы углерода остаются в решетке. Эти атомы, как упоминалось выше, слишком велики, чтобы поддерживаться решеткой ОЦК, поэтому она существенно искажается, что переводит решетку ОЦК в тетрагональную (прямоугольный параллелепипед) решетку или мартенсит. Этот закаленный мартенсит, случайно набитый атомами углерода, не является термически стабильным. Эта решетка стремится иметь множество пустот в упаковке своих атомов, что делает ее твердой, но сравнительно хрупкой. Для улучшения качества стали производится ее отпуск. Если требуется высокая прочность №416, отпуск, производимый при 450°-700°F, обеспечивает предел прочности в 160000-220000 psi (1176-1617Мпа) и твердость по Роквеллу в 35-45 единиц. Ствольные стали, тем не менее, лучше делать с HRC 28-32, то есть отпускать их при температуре около 1050°-1100°F (в общем, при повышении температуры отпуска мартенсита получается более мягкий, менее прочный и более упругий металл), что дает предел прочности порядка 120000-140000 psi (882-1029Мпа) при пределе упругости 100000-110000 psi (735-808,5 Мпа). Такой отпуск при 1050°-1100°F также используется для снятия напряжений после формовочных операций, таких как прогон дорна через ствол.
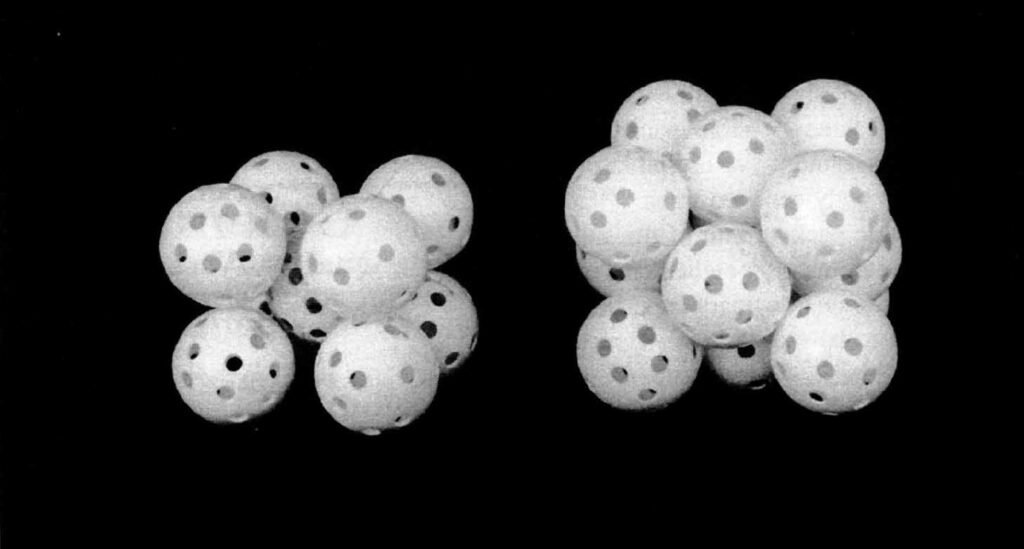
С целью визуализации атомной упаковки на Рисунке 1 показаны модели объемно-центрированной кубической решетки, которую я сделал из пластиковых мячиков (похожих на мячи для гольфа), а также гранецентрированной кубической решетки. Это структурные единицы, которые простираются в трех направлениях в каждом зерне феррита и аустенита. Справочник Краусса, указанный выше, описывает в деталях решетки ОЦК, ГЦК и ОЦТ.
Вот важный аспект по включениям MnS в сталь№416. Когда отливаются чушки, застывая из расплавленного металла, гранулы металла и сульфида кристаллизуются до определенного размера зерен. При обработке чушек в прутки металл обрабатывается горячим, и все гранулы деформируются. Тем не менее, зерна металла восстанавливаются после обработки в равноосные гранулы, тогда как гранулы сульфида нет. Таким образом, крупнозернистые включения MnS из чушки обретают свой нормальный размер зерен (хотя их форма удлиняется) на всем пути к мастерской ствольного мастера.
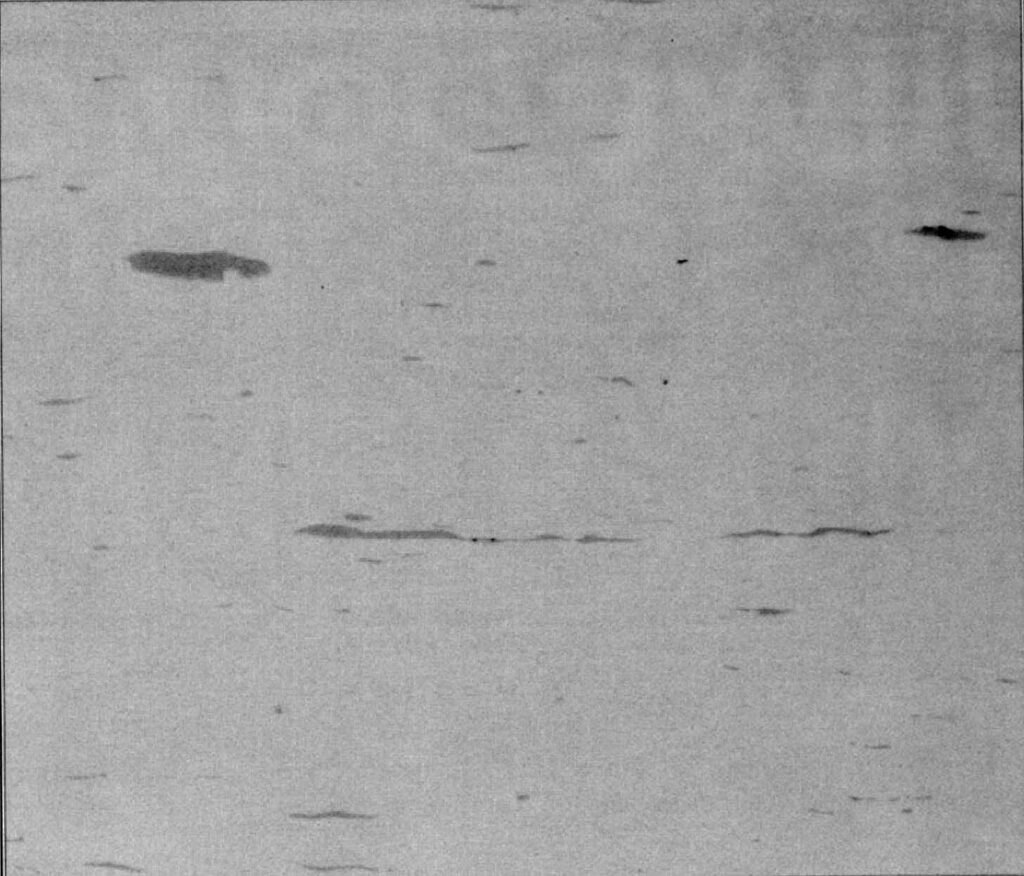
На Рисунках 2 и 3 показана микроструктура стали №416. этот образец получен из дульной части ствола Krieger под патрон .220 Swift длиной 26”(660 мм). Этот ствол отстрелял 1325 выстрелов, в основном по степным собачкам при температуре около 90°-100° градусов. Он давал прекрасную точность, даже несколько попаданий на 500-600 ярдов (452-570 м). На Рисунке 2 показаны продолговатые зерна (называемые металлографистами «стрингеры») MnS, вытянутые вдоль длинной оси ствола, имеющие около 0,001”-0,005”(0,0254-0,127мм) длины. Как мы обсудим ниже, такой размер зерен является максимально допустимым. На Рисунке 3 показан металл ствола при увеличении 500 крат (столбик в 20 микрон = 0,0008”), протравленный специальным раствором, чтобы показать детали микроструктуры. Большая часть разреза состоит из средне серых зерен, которые были аустенитом и превратились в мартенсит в процессе закалки. Каждое бывшее аустенитовое зерно (все связи внутри которого сохранились) теперь состоит из массы взаимно параллельных мартенситовых зерен в форме реек. Мы также должны заметить, что мартенситовая структура в основном сохраняется даже после отпуска при 1050° (дающего уменьшение твердости до HRC32 и повышающего упругость), и здесь мы как раз видим «отпущенный» мартенсит. Видны два темно-серые зерна сульфида, с находящимися рядом несколькими продолговатыми зернами дельта-феррита – объемно-центрированной фазы, присутствующей в некоторых №416 и остающихся в результате небольших проблем при термоупрочнении на металлургическом заводе. Заметка: эти микрофотографии любезно предоставлены металлографистом Г.М. Лукасом из Buehler Ltd, крупнейшей мировой компанией по оснащению металлографическим оборудованием и материалами.
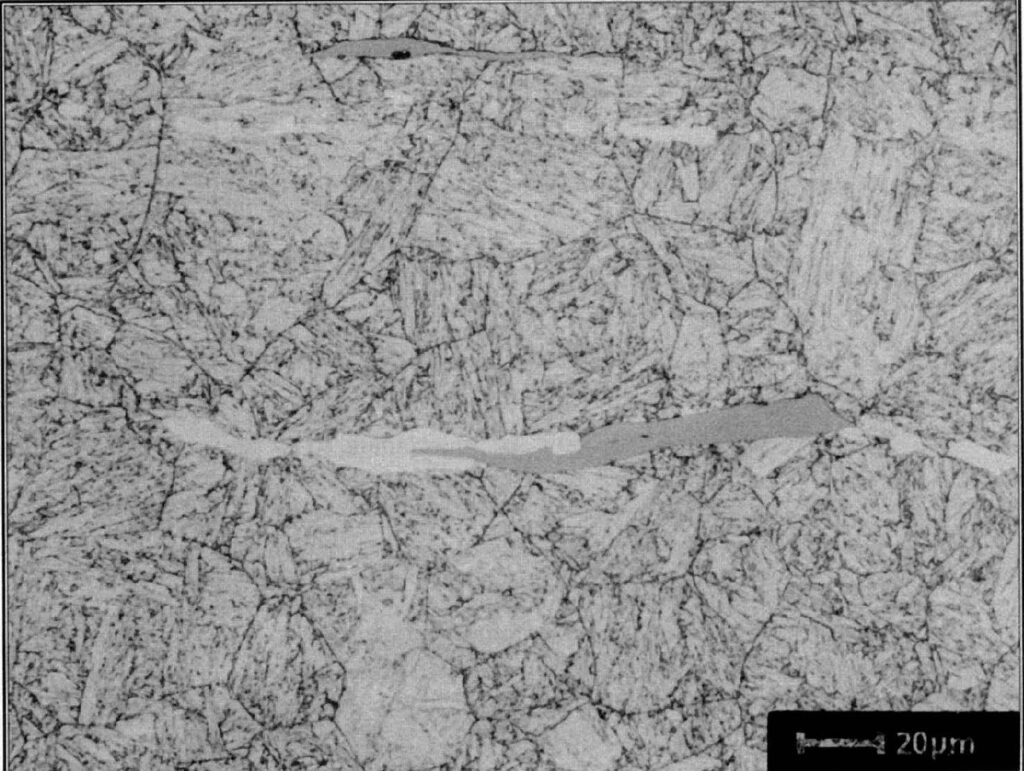
Надо отметить широко распространенное неправильное использование людьми слова «кристаллизация» в отношении металлов на протяжении многих лет. Если кусок стали, меди или алюминия попеременно сгибать назад и вперед до тех пор, пока он не сломается (это называется «холодная обработка»), они могут сказать, что он «кристаллизуется». Это абсолютно не правильно. На самом деле происходит вот что – крошечные кристаллические частицы в металле сильно деформируются и искажаются в процессе холодной обработки, эти гранулы противостоят деформации при помощи движения нерегулярностей упаковки атомов их кристаллической решетки (называемых учеными-металлургами «дислокациями»), до разделения, происходящего при аккумуляции дислокаций, в конечном счете, до точки излома. Холодная обработка, кстати, делает латунь и другие медесодержащие сплавы тверже.
Охрупчивание стали № 416 ПРИ 885°
Многие стали становятся хрупкими при разным температурных режимах. Для №416 это происходит при отпуске в диапазоне 750°-1050°F, в районе, где сопротивление удару резко уменьшается, совместно с вязкостью, электрическим сопротивлением и коррозионной стойкостью. Это происходит благодаря преобладанию очень мелкой богатой хромом фазы ОЦК.
Холодное охрупчивание
Мартенситовые нержавеющие стали класса, в котором находится и №416, показывают резко выраженную тенденцию к охрупчиванию (или нехватку упругости) при низких температурах. В общем, все стали мартенситового или ферритового типа (т.е. имеющие объемно-центрированную структуру решеток) проходят переход их вязкого состояния к хрупкому при падении температуры. Хрупкость измеряется при помощи простых приборов двух типов, в которых молотообразная головка на маятнике ударяет по зазубренному прутку, поддерживаемому либо с одного, либо с двух концов. Энергия, требуемая для разделения тестового образца, определяется в диапазоне температур от чуть выше комнатной до ниже -200°F для некоторый стальных сплавов.
При таких проверках энергии удара, уменьшающиеся с повышением хрупкости, обычно уменьшаются до величин, составляющих всего 10%-15% от энергии при более высокой температуре, для диапазона уменьшения температур в 150°-200°F. Поверхность разлома, происходящая от повышенного напряжения, возрастает от волокнообразной зарубки (или вязкой от срастания микропустот) при повышенных температурах до раскола (кристаллический, хрупкий разлом) при пониженных температурах. Переход от вязкого к хрупкому для нержавеющих сталей №410 и №416, отпущенных до HRC30, может быть сдвинут до температур 200°…-50°F и даже до -100°F с точкой перехода от вязкой к хрупкой фракции при 40°…80°F. Для контраста, хромомолибденовая сталь №4130 будет переходить от вязкого к хрупкому состоянию при — 100°F и ниже. Такое сравнительно хрупкое поведение стали №416 при холодных и минусовых температурах может быть не очень хорошо известно стрелкам из винтовки, но я обращаю ваше внимание, что изготовитель стволов Джон Криегер (Krieger) отказался от изготовления стволов спортерного веса из №416 (он прислушался к своим советникам-металлургам!). Кроме того, я бы ни за что не хотел иметь даже детали от винтовки, механизм которой изготовлен из стали №416 или ее близкого по составу отливки сородича (серосодержащие стали не могут быть правильно отлиты, потому что сера служит причиной странных вещей, происходящих с микроструктурой металла при его застывании) для использования в холодных погодных условиях. Стрелки, желающие иметь не коррозирующую затворную группу для использования зимой за Фэирбэнксом и Йеллоунайфом должны выбирать один из титановых сплавов, который обеспечивает прекрасную работу при сильных морозах.
Околодульные раковины на стали № 416
Охрупчивание нержавеющей стали №416 при низких температурах и при отпуске в диапазоне от 750° до 1050°F характеристики известные, они возникают на любых партиях стали №416, и обычно их избегают или отрабатывают. Тем не менее, существует более коварная проблема с некоторыми партиями стали №416, которую изготовители стволов и некоторые целевые стрелки расплывчато осознают на протяжении многих лет. Она состоит просто в наличии чрезмерно больших зерен MnS, возникших из-за дефектов металлургического предприятия, и проявляется в образовании раковин около и на дульном срезе ствола (смотри ниже). Существует другая возможность, о которой я слышал, но никто ее пока документально не подтвердил: эти стрингеры или концентрации зерен MnS вдоль оси ствола вероятно возникают из-за того, что расплавленный металл вначале отливают в чушки (вспомните, что сульфидная фаза кристаллизуется из расплава последней). Эти концентрации сохраняются при протяжке чушек в прутки. Изготовители стволов также заявляют о редких случаях, когда твердость прутка изменяется по его длине, что может происходить из-за вариаций в содержании углерода. Дорнование такого ствола дает разницу в диаметре канала ствола из-за кольцевого распределения напряжений в окружающем канал металле, находящегося в прямой пропорциональности от твердости (и отсюда прочности), а кольцевая деформация приводит к переформованию металла (и диаметра канала ствола) после прохода дорна.
Позвольте мне подчеркнуть, что изготовители стволов полностью зависят от производителей стали (как некоторые говорят, от их милости), чтобы получить сталь — однородную, достаточно мелкозернистую, закаленную и отожженную в соответствии со спецификацией, и нужной твердости. Большинство ствольщиков имеют приспособления для измерения твердости, но они не могут проверить каждую партию полученной стали и изучить ее микроструктуру под микроскопом.
Возвращаясь к околодульным раковинам из-за очень больших включений MnS, вот несколько конкретных стволов, сделанных из стали с таким дефектом, приведенные анонимно для защиты интересов первоклассных изготовителей стволов и сталелитейных компаний, контроль качества которых, в целом, удовлетворительный. Очень опытный механообработчик и спортсмен-бенчрестер, который теперь только изготавливает целевые винтовки и сопутствующие принадлежности, недавно изготовил винтовки для стрельбы на 1000 ярдов под один из 6,5 мм патронов для четырех стрелков. Этот оружейник, как и большинство других, использует кустарные стволы от разных производителей в соответствии с запросами своих клиентов. Так случилось, что все четыре ствола для этих винтовок были изготовлены одним и тем же престижным производителем и все куплены в течение четырех недель у этого производителя. (И я понимаю, что два других изготовителя стволов получили заготовки из той же самой партии стали). Две из этих винтовок имели кустарные ресиверы, а еще две имели тщательно спроектированные заводские ресиверы. Все ресиверы были свободно вывешенными, и каждый ствол был block bedded (закреплен в блоке) с использованием сталенаполненной эпоксидной смолы и алюминиевых вкладышей (pillar) под блоками для четырех крепежных болтов. Каждый ствол был «обкатан» (если этот термин можно здесь применить) обычным образом – чистка после одного выстрела, и последующие выстрелы с частой чисткой. Каждый ствол показывал минимальное загрязнение металла и чистился просто. Все четыре винтовки группировали 5-патронные группы в 0,2-0,4 МОА с 140 и 142-грановыми пулями после подбора правильного заряда. Чем дальше, тем лучше; но приблизительно на 100-125 выстрелах все стволы начали давать один из трех либо один из пяти отрывов в группах и загрязнение оболочками пуль в дульной части существенно возросло. Первые два ствола, которые начали так вести себя, были возращены оружейнику, и он проверил их с помощью бороскопа Hawkeye (смотри ниже) и еле разглядел очень тонкие раковины в дульной части канала ствола. Он также спросил меня, что могло вызвать такое состояние. Я высказал обычное (для меня) предположение о включениях MnS, и добавил, что для того, чтобы все выяснить, необходимо отполировать разрез стали и рассмотреть его под микроскопом со 100 кратным или более увеличением. Зерна MnS темно-серые и хорошо видны на полированном разрезе (см. Рисунок 2). Итак, мы послали кусочек среза с дульной части для консультации металлургу, который 1) посмотрел на поверхность канала ствола в бинокулярный микроскоп при 25 и 50 кратном увеличении и подтвердил наличие раковин.; 2) подготовил полированные срезы параллельно и перпендикулярно оси канала ствола и при помощи микроскопа разглядел в зерна MnS в параллельном оси срезе, которые имели в длину 0,003”-0,004”(0,0762-0,1016 мм) и 3) измерил площадь гранул MnS в разрезах, получив 0,82%. Предположив, что процент по площади равен проценту по объему, и что сульфид только марганцевый, я рассчитал, что содержание серы составило около 0,016% — или допустимое значение. Важным результатом для металлургического расследования было то, что размер зерен MnS в шесть-восемь раз превосходил указанный в справочном образце №416.
Затем я решил проверить другие два ствола с раковинами при помощи моего бороскопа Hawkeye. В каждом оказалось множество раковин, самая большая около 0,005”(0,127 мм) в ширину (я не мог оценить ее глубину). Такой размер зерен соответствует размеру зерен MnS. Эти раковины распространялись на 9”-10”(230-250мм), пока не прекращались. Ствол в начале нарезов не показывал признаков раковин. Что стало причиной появления раковин? Скорее всего распад зерен MnS. Их расположение только возле дульного среза любопытно: единственное разумное предположение связано у меня с нагревом пули в результате трения. В рассказе о зависимости точности от загрязнения (PS, Февраль 2000) я сделал приблизительные расчеты и нашел, что наружная температура (температура оболочки) пули может достигать 1300°F или около того на дульном срезе. В следующем выпуске PS другой автор Гарольд Вогн описал измерение температуры в 1400°F в канале ствола калибра 7,62мм после выстрела. Он дискутировал о важности загрязнения в дульной части ствола. Так как очень горячая оболочка пули проходит через зерно сульфида, она нагревает очень тонкий слой зерна до температуры распада (весь класс сульфидов металлов показывает очень плохую температурную стабильность) и эти атомы вылетают, обеспечивая вырастание раковины. Более того, пули с длинными телами, такие как 140 и 142-грановые пули, использовавшиеся в этих 6,5 мм стволах, будут находится в контакте с любой точкой ствола дольше, чем короткие пули. Такой эффект нагрева оболочки пули и образования раковин будет максимален при длинных пулях и стволах, используемых стрелками на большие дальности. Бенчрест стрелки на короткие дистанции, использующие 21”-22”(533-558мм) стволы и короткие пули, должны наблюдать намного меньшее (или никакого) околодульного раковинообразования на стали №416, содержащей такие чрезмерно большие зерна MnS. Кроме того, передача тепла от оболочки пули включениям MnS будет происходить только на чистых стволах; слой загрязнения будет поглощать тепло и предохранять от распада зерна сульфида. В последнее время должно находится много стволов из такой плохой стали в использовании у ничего не подозревающих стрелков.
Я также думаю, что около дульное образование раковин возникает во всех стволах из стали №416, но эти раковины имеют обычно не более одной или нескольких десятитысячных дюйма в диаметре, и они не на столько велики, чтобы ухудшать кучность или быть причиной необычного загрязнения от оболочек пуль.
Несколько опытных стрелков спрашивали, может ли покрытие пули с MoS2 быть причиной образования раковин около дульного среза в этих четырех стволах. Один из стволов стрелял только пулями без покрытия. Более того, любые плохие вещи, которые могут произойти с молибденом (такие, как разложение сульфида на металл Мо и серу) должны происходить только на первых нескольких дюймах прохода пули, где температура горения пороха около 4000°-5000°F, а не на выходе из ствола.
Долговечность ствола из стали № 416
Могут ли стволы из стали №416 быть долговечней, чем такие же из хромо-молибденовой стали? Читатели PS со стажем знают, что мнения по этому вопросу разделились. Факт, что ствольный металл может быть коррозионно-стойким на воздухе при комнатной температуре противопоставляется тому, что район пульного входа подвергается воздействию очень высоких давлений и температур горения пороха, и там возникают условия распада. Разгар ствола происходит из-за процесса, когда горячие пороховые газы являются причиной образования слоя нитрида железа на поверхности канала ствола, и такое растрескивание и скалывание хрупких нитридов является основной движущей силой разгара (см. мою статью в Октябрьском 1999 года выпуске PS). И железо и хром (также как и молибден) являются готовыми формирователями нитридов, поэтому Fe-Cr содержащая сталь №416 будет также восприимчива к нитридообразованию, как любая из легкосплавных хромо-молибденовых сталей. Кобальт и никель же не образуют нитридов, поэтому вкладыши в пульные входы пулеметов изготавливают (с большим трудом и материальными затратами!) из сплавов на основе кобальта, таких как Stellite, обеспечивающих несравненный срок службы. Роль включений MnS в разгаре пульного входа хорошо не изучена: они, возможно, разлагаются и производят раковины в местах, где начинается растрескивания соседнего слоя нитрида. Стволы из нержавеющей стали №410 (то есть той же №416, но без серы) могут служить дольше, но этот металл труднее обрабатывать – как №17-4 и другие дисперсионно-твердеющие нержавеющие стали – и не применяются для изготовления точных стволов. Так как титан является отличным формирователем нитридов (свидетельство – сверла с покрытием TiN, доступные в любом хозяйственном магазине), титановые стволы также будут откладывать нитридные пленки на своих пульных входах. Нержавеющие стволы без содержания серы, изготовленные высокотехнологичными методами обработки – особенно электроэррозией? Керамические стволы? Стальные трубки, покрытые толстым слоем сплава на основе кобальта и затем обработанные развертками с последующим изготовлением нарезов — возможность, о которой говорил мне эксперт по ремонту стволов Клифф ЛаБаунти (Cliff LaBounty)?
Преемник стали № 416?
Я не думаю, что вскоре может прийти что-то на замену. Тем не менее, если наши сталелитейные заводы могут сохранить размер зерен в №416 на минимуме – для тех же сульфидов менее чем несколько десятитысячных дюйма – мы, стрелки, будем счастливы использовать ее.
Журнал «Precision Shooting»,
Фред Баркер